اتصل
هاتف
+0086-371-86162511
عنوان
تشنغتشو ، الصين
Common Failure Of Jaw Crusher
Failure Analysis of Jaw Crusher China Crusher Mesto,
Failure cause: the hardness or toughness of the broken material exceeds the range specified in the operation manual; the reverse connection of the motor power makes the main engine start in reverse Failure analysis of jaw crusher and its components using ANOVA Journal of the Brazilian Society of Mechanical Sciences and Failure analysis of jaw crusher and its components
Failure analysis of a crusher jaw ScienceDirect
The study revealed that the failure of locally produced crusher jaws was not due to wrong chemical composition but to the precipitation of carbides at grain Determination of the optimal angle of inclination of the toggle plate, development of jaws with varying wear rate along the crushing chamber, and development of comminution energy models (PDF) DESIGN AND OPERATIONS CHALLENGES OF A

Failure rate analysis of Jaw Crusher: a case study
Failure of crusher components has considerable influence on the productivity of a crushing plant In order to improve performance and operational reliability, its critical components are neededThis paper considers the methods for analysing failures of jaw crusher and its critical components in a mineral processing plant using statistical tools namely life Failure analysis of jaw crusher and its components using

Failure rate analysis of Jaw Crusher: a case study Springer
The present study has examined failures of jaw crusher and its components in a major mineral pro cessing plant The failure data of two year duration are recorded from the This paper considers the methods for analyzing failure rates of a jaw crusher and its critical components application of a twoparameter Weibull distribution in Failure rate analysis of jaw crusher using Weibull model
Common Fault Causes And Solutions of Jaw Crusher
This article shares common problems in several types of bearings, brackets, frames, etc, and analyzes the reasons and solutions 1 Bearing failure A Bearing damage Insufficient lubrication of bearings and untimely maintenance, resulting in poor lubrication; too large feeding height causing the movable jaw to be impacted; Feed shock oftenIn this article, we will introduce the common fault causes and troubleshooting methods of the jaw crusher: Fault: The flywheel rotates but the moving jaw stops swinging Causes: 1The thrust plate is broken; Common failure reasons and elimination methods of
Failure rate analysis of Jaw Crusher: a case study Sādhanā
Failure of crusher components has considerable influence on the productivity of a crushing plant In order to improve performance and operational reliability, its critical components are needed to be identified to make replacement in time before any catastrophic failure happens Though traditional maintenance practices exist in crushing Dragline with a boom length of about 96 m and bucket capacity of around 24 m3 are most common Sudden failure of any of its subsystem will stop the machine from functioningA double toggle jaw crusher Download Scientific Diagram
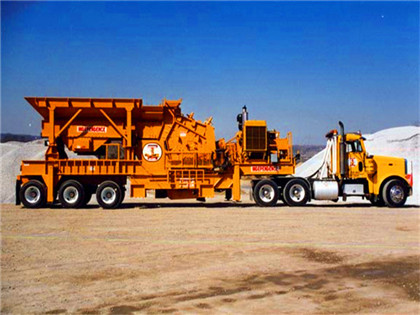
common failure of jaw crusher
Failure Analysis of Jaw Crusher July 07, 2021 Jaw crusher is the key crusher equipment for stone crushing production Many customers will meet various kinds of fault problems during production process, which will affect the whole production schedule Here, We summarizes the common failure and treatment of the jaw crusher 1In addition to the wear problem of the jaw plate, there are many other problems caused by parts and components can not be ignored Next, we will introduce the failure analysis and troubleshooting of the jaw crusher The main engine suddenly stopped Cause analysis: 1 The discharge port is blocked, causing full cavity blockingCause Analysis and Problems Solving of Jaw Crusher
Experimental and Numerical Studies of Jaw Crusher Supporting
common use of sophisticated experimental and numerical techniques [3] and [4] failure Fig 2 Jaw crusher layout (supporting structure highlighted in red, marked with arrow)Improperly adjusted or worn out bearings: If the bearings that support the jaw are not adjusted properly or have worn out, it can cause excessive stress on the toggle plate, leading to its failureWhat causes the jaw crusher toggle plate to break? LinkedIn
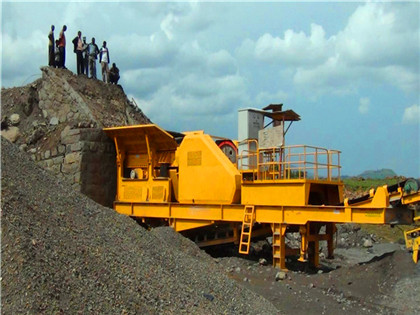
Jaw Crusher an overview ScienceDirect Topics
The capacity of jaw crushers is a measure of the mass or volume of crushed material produced in unit time of operation The capacity is primarily a function of: 1 crusher design characteristics such as width and depth of the crushing chamber, 2 The failure rate increases as the crusher ages and wears,so diagnosis and fault prediction are essential actions to assess the condition of equipment and optimize its use In [ 53 ], analyses based on physical models, knowledgebased models, and artificial intelligence models were proposed for diagnosisModeling and Improving the Efficiency of Crushing Equipment

What Is a Jaw Crusher? Sandrock Mining
A jaw crusher is a machine that breaks down big rocks into smaller ones It has two jaws, one fixed and the other moving, that work together to crush the material The fixed jaw is mounted on a frame and cannot move, while the moving jaw is connected to an eccentric shaft Jaw crushers are used extensively in the mining, quarrying, andPerforming regular maintenance on crushers is integral to the reliability, performance and output they achieve Prevention is better than cure; by carrying out regular inspections, an aggregate producer will Failure to maintain crushers has a high price Quarry

Lifetime Prediction for the Jaw Crusher by the Criterion of Toggle
General view of the PE 1200 × 1500 jaw crusher (a), a structural diagram of the crusher (b), a threedimensional model of the toggle (c) Full size image The average lifetime of the jaw crusher toggle can be determined by two methods: with the use of the failure model developed ( 2 )–( 5 ) and on the basis of SNCurves [ 20 22 ]Preventive maintenance is usually set up on a daily (8 hours), weekly (40 hours), monthly (200 hours), yearly (2,000 hours), and liner change schedule Following the scheduled checks and inspections, adjustments are made and worn parts are replaced before a major crusher breakdown occurs Preventive maintenance is a key component Understanding three different types of crusher maintenance

Common Faults of Impact crusher Crusher Blog
First,impact crusher vibration 1 the material is too large, you can check the feed size 2uneven wear, indicating the need to replace the hammer back, 3 rotor imbalance, the need to adjust 4based handled properly, need to check the anchor bolts and reinforcement This professional crusher blog contains crusher basics which focuses A crusher jaw that had failed while in service was studied through metallographic techniques to determine the cause of the failure Our investigation revealed that the reason for the fracture was the presence of large carbides at the grain boundaries and in the grain matrix This led to the formation of microcracks that propagated along theA Study of Premature Failure of Crusher Jaws SpringerLink
Experimental and Numerical Studies of Jaw Crusher Supporting
Natural frequencies of the crusher’s supporting structure No of natural mode Frequency [Hz] 1 339 2 596 3 1450 Fig 9 Natural frequency mode shape of the crusher’s supporting structure Mode 1 The next step was to perform fatigue calculations Considering that dynamic forces are created in the jaw area of the crusher unit, loads in bothAnd cone crusher can be used for shaping because of the adoption of lamination crushing principle, which makes the final products have good cubical shape 8 Different in prices Due the structures and features, cone crusher is much more expensive than jaw crusher 9 Different in maintenance costsJaw Crusher VS Cone Crusher: 9 Key Differences

Minerals Free FullText DEM Simulation of LaboratoryScale Jaw
For articles published under an open access Creative Common CC BY license, any part of the article may be reused without permission provided that the SA Failure analysis of a crusher jaw In Handbook of Materials Failure Analysis; ButterworthHeinemann: Oxford, UK, 2018; pp 187–207 ISBN 83 [Google ScholarDragline with a boom length of about 96 m and bucket capacity of around 24 m3 are most common Sudden failure of any of its subsystem will stop the machine from functioningOutput data of jaw crusher Download Table ResearchGate